Soft ore offers Sarytogan Graphite big savings at Kazakh graphite project
- Doug Bright
- 11 hours ago
- 3 min read
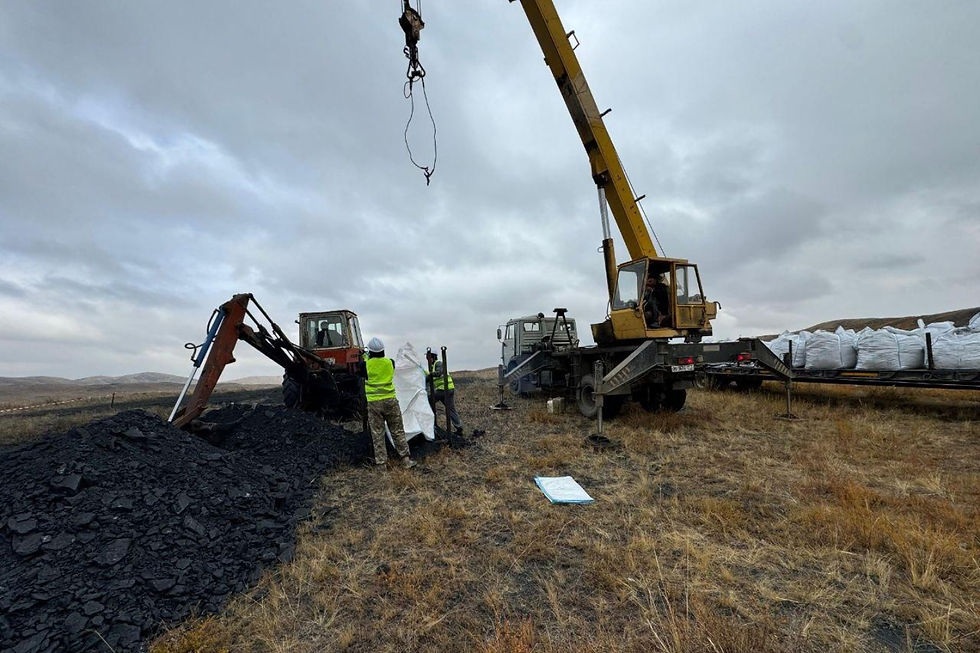
Pilot milling tests on a trial bulk 10-tonne sample from Sarytogan Graphite’s (ASX: SGA) deposit in central eastern Kazakhstan show the graphite ore is softer than assumed for the company’s pre-feasibility study.
The findings should improve the numbers in the definitive feasibility study for the project.
Sarytogan should be able to reduce the installed mill power required by 65 per cent, which would flow-on to a 36 per cent cut in the overall power it will need for grinding the ore to size.
The company should be able to achieve other operational efficiencies – which will save on production costs.
The pilot test work was undertaken on material drawn from 24t of sample material excavated last September by backhoe from surface outcrop.
The upper 3 metres was bogged out and set aside for subsequent site rehabilitation and to access underlying unweathered lump graphitic ore at an average grade of 33 per cent total graphitic content (TGC).
The average grade was established from grab sampling of material from a series of 1t bags of bulk sample, which delivered assays from 27 per cent to 41 per cent TGC.
Eight tonnes of the bulk sample were retained as back-up material, while the remaining 16t were crushed to pass 5 millimetres before they were blended as feedstock for trial milling.
The metallurgical test work was conducted by KazHydroMed LLP laboratory, based in the nearby regional capital Karaganda, under Australian comminution expert Dean David’s supervision.
Milling involved a 95 centimetre by 78cm ball mill operating in closed circuit using a hydrocyclone to separate solid particles based on their size and density from a liquid stream. The power demand was measured while running the mill with no load and during each milling trial and size measurements were acquired at the end of each key test phase.
Initial tests at a feed rate of 300 kilograms per hour, 500kg/hr, 700kg/hr and 800kg/hr showed a pilot mill feed rate at 317kg/h is optimal to achieve a target sizing of 95 per cent passing 106 microns (0.106mm).
That initial test phase was followed by milling runs at the optimal 317kg/h feed rate to determine a definitive operating work index for the project.
The index of 6.05 kilowatt hours per tonne confirmed the ore is very soft and considerably softer than all previous assumptions.
This pilot scale milling test has demonstrated the low milling costs of our very soft Sarytogan Graphite ore. It highlights one of the main strategic advantages of Sarytogan; being able to go straight to fine microcrystalline graphite without expensive regrinding. Furthermore, the proper conservatism of the PFS is evident, with these measurements expected to support cost reductions to be incorporated into the DFS.
Sarytogan Graphite Managing Director Sean Gregory
Sarytogan views the operating work index for its graphite from its pilot-scale wet milling as a more reliable measure of comparative ore hardness and grindability.
It says the alternative of dry milling could result in the graphite adhering to and thickly coating the surface of the grinding media, which would reduce the mill’s effectiveness and lead to biased results. Dry milling could also blind the product sizing screens used for testing.
The impressive wet milling findings will flow on to significant savings in crushing requirements and eliminate the need for jaw and cone crushers from the initial prefeasibility study, enabling Sarytogan to replace the equipment with lighter-duty units such as toothed-roll crushers.
The latest 317kg/h test result suggests Sarytogan can use a much smaller ball mill with an installed motor power of about 175 kiloWatts and a net power of 150kW, amounting to 65 per cent and 36 per cent reductions respectively compared to the company’s pre-feasibility study.
Other significant cost savings include reduced maintenance due to reduced wear on components and less risk attaining optimal use of the grinding circuit.
Sarytogan can optimise mill-feed preparation by properly tailoring the equipment to the soft ore, leading to improved downstream performance, higher productivity and reduced downtime.
The company plans to send about 700kg of the milled ore to Australia to generate more bulk flotation concentrate. In 2023, the company similarly treated a 60kg sample to produce 20kg of concentrate.
The previous test work achieved a concentrate grade of 81.4 per cent TGC at 84.4 per cent recovery from a representative composite sample drawn from eight diamond drill holes from the project’s northern and central graphite zones at a head grade of 32.5 per cent TGC.
After flotation test work is complete, final concentrate samples will be available for vendor test work using equipment designed for thermal purification, size classification and spheronisation. More importantly, the final work will also produce samples that Sarytogan can send to its customers.
Is your ASX-listed company doing something interesting? Contact: office@bullsnbears.com.au